Заводы, где грохот металла слышен только в кино, станки без оператора, а сложнейшие детали почти сразу идут к клиенту — звучит как фантастика, да? Но именно такую картину рисует машиностроение завтрашнего дня. Автоматизация, робототехника и зелёные технологии настолько стремительно ворвались на предприятия, что за ними не успевают даже профессионалы отрасли — не говоря уже о грандмастерах токарного дела прошлой эпохи. Представьте: еще пятнадцать-двадцать лет назад 3D-принтеры казались игрушкой. Сегодня ими печатают лопасти турбин для авиации. Машиностроение будто переживает вторую молодость: всё, что раньше казалось навсегда отлитым в железе, перезаписано, переосмысленно, полностью меняет своё лицо на глазах.
Глобальные драйверы перемен: что движет машиностроение сегодня
В основе перемен — не магия. Здесь работают вполне земные вещи: жёсткая конкуренция, нехватка специалистов, рост спроса на персонализацию и стремление компаний не отстать от цифрового мира. Почти каждый крупный международный производитель уже внедряет бережливое производство и цифровые двойники. Siemens, например, управляет своими заводами через цифровые «копии» цехов и конвейеров — на компьютере моделируются любые варианты, а потом они безболезненно переносятся на настоящие линии. Даже ремонт часто идёт удалённо: один инженер из Германии может решить проблему мотора на заводе в Китае через VR-очки.
Минимизация отходов — отдельная глава. Кто ещё десять лет назад говорил о возврате металлолома прямо с линии, вторичной переработке моторов и циклической экономике? Сегодня Toyota и Volvo отчитываются об экономии сотен тонн металла ежегодно именно за счёт рециклинга — к 2030 году они планируют, чтобы большая часть кузовных панелей делалась из переработанных материалов. Климатическая повестка неспешно, но неудержимо вторгается даже в те производства, где конкурентная борьба раньше шла разве что за толщину листа и износостойкость детали.
Но цифровизация цепляет не только заводы и линии. Она меняет подход к проектированию и тестам: компании создают цифровые прототипы, гоняют их в виртуальных аэротрубах и вибростендах с такой скоростью, что за один рабочий день можно проверить пару сотен гипотез. Когда появлялся электромобиль Porsche Taycan, ни одного «железного» прототипа не собирали вручную до самого запуска пилотной серии: все до последнего шурупа прогнали через компьютерные симуляторы.
Стремительно развивается рынок сервисов: необязательно быть владельцем завода, чтобы производить сложные компоненты — с помощью облачных платформ вроде Dassault Systèmes можно проектировать, тестировать и запускать в производство детали, находясь хоть на даче, хоть на другом континенте. Крупные компании и малые стартапы буквально в прямом смысле слова уравниваются в возможностях — кому есть идея, у того появляется шанс запустить свое детище в жизнь быстро и недорого.
Инновации и технологии: как меняются производство и продукты
Наверное, чаще всего за будущим машиностроения стоят три слова: роботизация, автоматизация и цифровизация. Причём не только там, где высокие зарплаты и дорогие роботы, но даже на вполне типичных российских предприятиях. В Перми недавно наладили массовое использование промышленных экзоскелетов для слесарей, позволяя женщинам и мужчинам с лёгкостью перемещать тяжелые узлы. В Казани интеллект-управление сварочными роботами снижает процент брака почти до нуля. На Урале машиностроительный завод оборудовал роботизированную линию, способную адаптироваться к выпуску новой продукции всего за сутки — раньше на это уходила неделя, а иногда и месяц.
Аддитивные технологии и, конечно, 3D-печать стремительно догоняют металлическую обработку и сварку. Уже сегодня детали для космоса (например, части двигателя «Союз») изготавливаются на 3D-принтере. Это не просто экономия времени и ресурсов: инженер создаёт модель, тут же «печатает» пробный образец, тестирует, и если надо — моментально дорабатывает. Такой подход практически убирает границы для экспериментов — даёт инженерам свободу и минимизирует брак.
Не обойти вопрос и по новым материалам. Лёгкие композиты, сверхпрочные полимеры, алюминиевые сплавы с памятью формы всё чаще сменяют традиционную сталь. Airbus и Boeing уже полагаются на детали из углепластика — это уменьшает вес самолёта, снижает расход топлива, делает авиаперевозки дешевле и экологичнее. В автомобилестроении благодаря композитам и сплавам автоконцерны выигрывают в цене, безопасности и долговечности машин.
Интернет вещей (IoT), искусственный интеллект и машинное обучение навсегда поменяли и наблюдение за оборудованием. Датчики на станках и конвейерах отправляют в облако всю информацию о температуре, вибрациях, нагрузке двигателя, а система сама анализирует: «Что-то не так — пора отправить мастера!» Заводы экономят на ремонтах миллионы — ведь теперь чинят станок не «по расписанию», а именно тогда, когда это реально нужно.
Автоматизация не стирает людей из профессии. Наоборот, работа становится интереснее — теперь не просто крутить гайки, а управлять «умными» линиями через планшет или VR-шлем. Но вместе с этим машиностроение требует новых навыков: нужны программисты, инженеры по системам управления, специалисты по data science — это совсем иная порода профессионалов, чем классические технологи начала века.
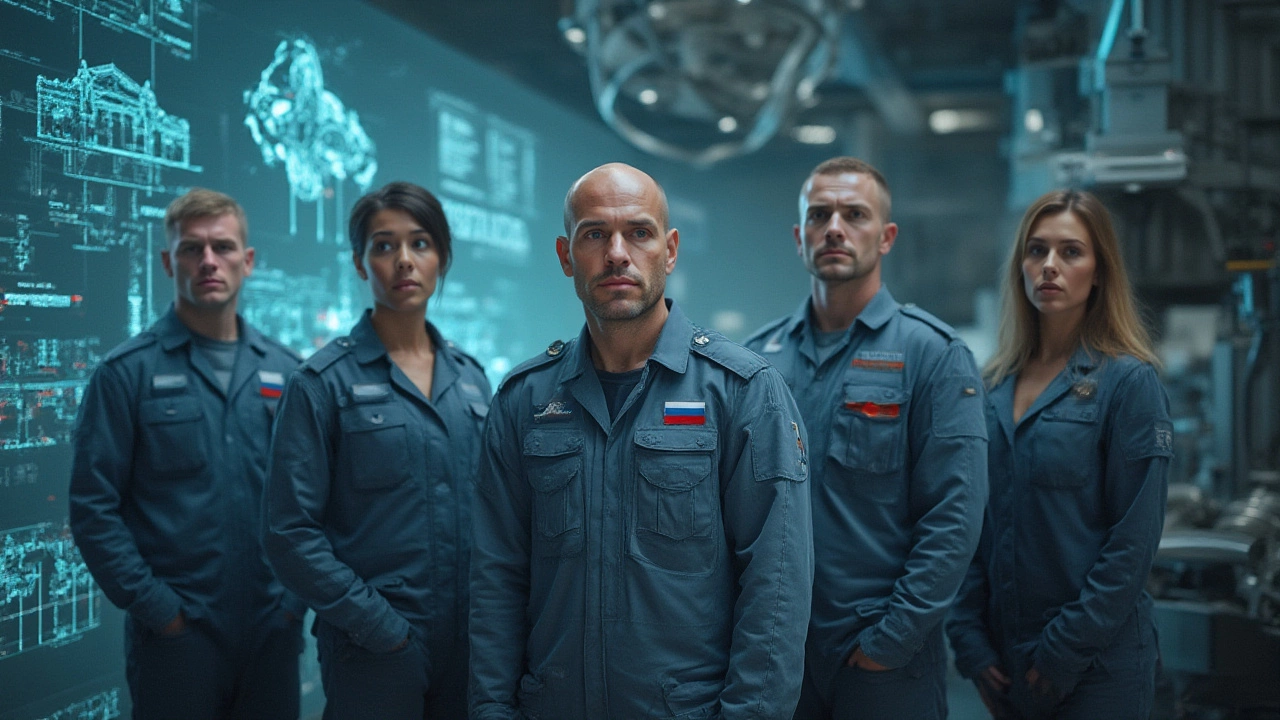
Новые профессии, вызовы и образование: кто нужен заводам будущего
Следующий оборот спирали — кадры. Уже сегодня заводы буквально соревнуются за молодых технических специалистов, а классические профессии быстро отходят на второй план. Токари, по-прежнему, на вес золота, но теперь ценятся не просто руки, а мозги: знания синхронизированных систем, навыки работы с Cobots (коллаборативными роботами), умение «читать» данные с цифровых двойников, быстро перестраивать производственные линии под новую задачу.
Инженеры-программисты и аналитики данных — самый горячий товар на рынке труда. Профессия «оператор цифрового производства» ещё десять лет назад звучала дико, сейчас это человек, управляющий всем предприятием через планшет или VR-шлем. Тренинги на Boeing проходят не на стенде, а в дополненной реальности — изучаешь, как чинить авиационный двигатель, надевая очки, и шаг за шагом повторяешь реальные операции.
Но переход завода к Industry 4.0 сопровождается сложностями. Переучивать взрослых работников непросто: представьте фрезеровщика с двадцатилетним стажем, который должен освоить работу с цифровым двойником своего станка или контролировать робота через приложение. Здесь важно, чтобы обучение было неформальным и без занудства — через практику, через работу на реальных задачах.
Большие компании инвестируют в внутренние академии, разрабатывают курсы по управлению данными, машинному обучению и IoT-технологиям совместно с техническими университетами. Даже государственные программы включают виртуальные тренажёры, междисциплинарные кейсы и проекты с реальным производством. Такие изменения дают результат: уменьшается текучка, проще внедрять новые технологии, появляется свежий взгляд на консервативные задачи.
Ключевая черта новых сотрудников — гибкость мышления и стремление учиться в процессе. Руководители успешных заводов сходятся в одном: будущий работник машиностроения — это немного айтишник, немного инженер, немного менеджер. Он реально понимает, как работает линия, что делать при сбое, какие данные собрать и куда их отправить, чтобы восстановить производство быстрее всех.
Тренды завтрашнего дня: отрасль-невидимка или двигатель прогресса?
Кто-то успокаивает себя — «машиностроение никогда не исчезнет, сталь всегда будет нужна», а кто-то верит — пальму первенства возьмут пробирочные материалы и полностью автоматизированные цеха. Но в одном сходятся все: отрасль уже совсем не та, что десять лет назад. **Будущее машиностроения** опирается не только на железо, но и на данные, синтетические материалы, IT-инфраструктуру.
Невидимые глазом изменения в производстве зачастую становятся видимыми только для самого завода и его клиентов. Потребители не видят интерактивные системы управления, цифровые кластеры и мозговой центр с десятками экранов — они получают результат: быструю поставку, индивидуальные решения, снижение стоимости и прогулку в сторону экологичности. Благодаря IoT, умным датчикам и цифровым платформам любой заказ — от сложного редуктора до индивидуального велосипеда — может быть собран и доставлен на порядок быстрее. Siemens к 2024 году сократил сроки проектирования некоторых компонентов на 80%.
Важный тренд — создание «умных фабрик» с распределёнными зонами и мгновенной сменой продукции. Представьте завод, который утром выпускает автозапчасти, а вечером — элементы для локомотива или ветроэнергетические турбины. Это уже не научная фантастика: в Китае такие фабрики работают в тестовом режиме. Они подстраиваются под ситуацию на рынке чуть ли не в реальном времени.
Не отстают и стартапы. Например, в Екатеринбурге небольшой коллектив инженеров с помощью 3D-принтера и искусственного интеллекта сделал пробную партию деталей для гоночных автомобилей и за месяц подписал контракт с крупным производителем спортивной техники. Подобные истории реальны — новые инструменты позволяют опережать гигантов, если идея стоящая и есть энергия довести дело до ума.
Самая необычная перспектива — удалённое производство сложных изделий на заказ в любой точке мира. Зачем возить моторы, если можно переслать цифровую модель на завод-партнер, и через сутки запчасть будет готова из местных материалов по стандарту клиента? За этим будущее — первые пилотные проекты уже есть в аэрокосмике, строительстве, медицине.
Перестанут ли люди работать руками? Нет, просто руки станут умнее, а голова — быстрее. Машиностроение всегда было «хребтом» индустрии, но теперь оно становится ещё и цифровым мозгом экономики. Кто научится объединять реальный и виртуальный мир — тот выведет свою компанию в лидеры. И поверьте, это касается не только гигантов, но и небольших мастерских. На арене остаются те, кто двигается вперёд, не зарываясь в металл, а строя новые смыслы.
Комментарии