Управлять качеством — это не просто проверять детали на брак. На заводах давно уже поняли: если просто надеяться на контрольщиков, проблем становится только больше. На деле система управления качеством начинается с самой идеи, как будет устроено производство, а не когда деталь уже сошла с конвейера.
В машиностроении под управление качеством обычно понимают всю цепочку — от выбора поставщика металла до упаковки готового изделия. Даже водитель, который перевозит продукцию на склад, становится частью этой системы. Каждый этап прописан в регламенте или стандарте, чтобы была прозрачность и контроль.
Есть полезный лайфхак: никогда не думайте, что контроль — это только обязанность отдела ОТК. Здоровая система учит всех замечать ошибки до того, как они станут проблемой крупнее. Поэтому грамотные руководители вводят простой принцип: увидел — сообщил.
- Что такое управление качеством на практике
- Кто отвечает за качество в цехе и офисе
- Документы, стандарты и контрольные точки
- Популярные ошибки и как не наступать на старые грабли
- Реальные советы по повышению качества
Что такое управление качеством на практике
Управление качеством в машиностроении — это не какая-то отдельная бумажная работа или раз в квартал внешний аудит. Это постоянная работа всего коллектива. Например, когда завод внедряет систему ISO 9001, речь идёт не только о бумажках на стене, а о реальных рабочих процессах, где роли чётко определены: кто что проверяет, кто за что отвечает, и кто исправляет, если что-то идёт не так.
На практике качеством занимаются не только контролёры, а абсолютно все: от слесаря до директора. Обычно система включает такие этапы:
- Установка чётких требований к закупаемым материалам (например, только металл определённой марки).
- Описание процесса сборки: шаг за шагом, чтобы никто не гадал что делать.
- Текущий контроль на линиях — то есть проверяют не потом, а во время работы.
- Учёт и анализ брака: завод не просто списывает детали, а реально разбирается почему так получилось.
- Запуск программы внутреннего обучения — чтобы новички не учились на ошибках, а знали, как их избегать.
Что интересно: статистика за 2023 год показывает, что 85% крупных российских машиностроительных заводов, где работает современное управление качеством, сокращают расходы на исправление брака минимум на 20%. Это реальная экономия и меньше головной боли на совещаниях.
Ещё важный момент — не надеяться на магию единичных проверок. Надёжная схема — это когда требования понятны, ошибки быстро замечаются, а сотрудники не боятся сообщить о проблеме. Такой подход реально работает и снижает риск крупных потерь.
Шаг системы качества | Что даёт |
---|---|
Контроль входящих материалов | Меньше брака и простоев |
Промежуточный контроль | Выявление проблем сразу |
Обучение персонала | Снижение несчастных случаев и ошибок |
Поэтому управление качеством — это не разовая акция, а рутинный, но полезный процесс, который реально улучшает итоговый продукт.
Кто отвечает за качество в цехе и офисе
Многие до сих пор верят, что за управление качеством в машиностроении отвечает только отдел контроля или главный инженер. На практике всё намного шире. По современным стандартам ISO 9001 и ГОСТ — за качество отвечает вообще каждый, кто как-то участвует в процессе.
Начнём с производства. Операторы станков следят не только за точностью, но и за чистотой рабочего места, правильным хранением заготовок, вовремя сообщают о сбоях. Бригадир — это человек, который видит картинку целиком, быстро реагирует на отклонения, организует доппроверки.
Дальше идут мастера и технологи. Они составляют маршруты, обучают новых сотрудников и собирают обратную связь. Технический контроль (ОТК), конечно, не уходит: его задача — ловить то, что не увидел станочник, но не подменять собой всю систему.
В офисе всё не так скучно, как кажется. При закупке материалов специалист по снабжению проверяет сертификаты, просит образцы и смотрит на отзывы других заводов. Бухгалтер отвечает, чтобы счета оплачивались только надёжным поставщикам, а юрист — чтобы контракты позволяли отслеживать качество.
Если описывать цепочку ответственности, получится примерно так:
- Работник у станка — первый, кто может поймать ошибку;
- Бригадир — тот, кто контролирует выполнение технологий;
- Технолог и мастер — люди, поддерживающие стандарты и оптимизирующие процессы;
- ОТК — финальная проверка, но не единственный фильтр;
- Снабженец, бухгалтер, юрист — обеспечивают входной контроль и юридическую чистоту;
- Начальник производства — тот, кто объединяет всю схему и делает выводы при проблемах.
В 2023 году российские машиностроительные компании в системах управления качеством перестроились так, что участниками стали около 70% сотрудников, а не только специалисты ОТК. Это сильно подняло уровень самоконтроля на местах.
Так что, спрашивая «кто за что в ответе?», правильный ответ — все, кто имеет дело с деталью или документом хотя бы один раз.
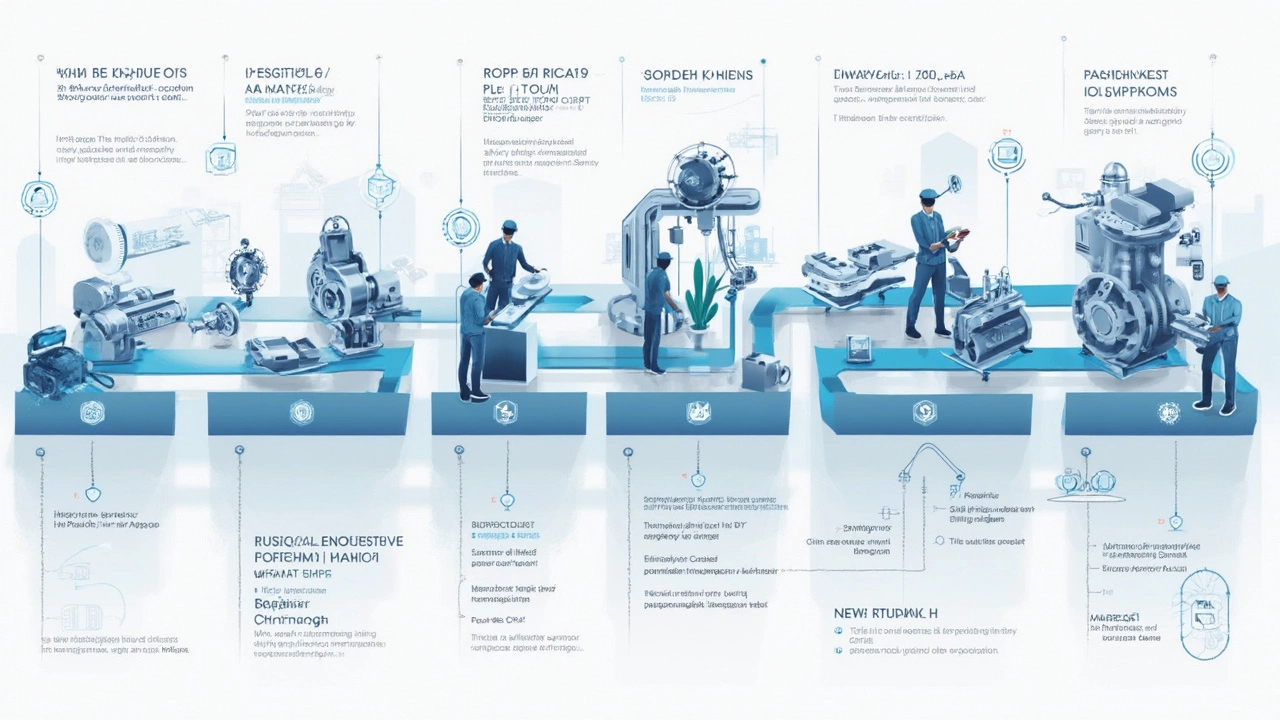
Документы, стандарты и контрольные точки
Без документов никакая система управления качеством не заработает нормально. Всё начинается с ГОСТов, ТУ, чертежей и инструкций. В машиностроении эти бумаги – не формальность, а инструкция к выживанию: любой отступ – и партия может уйти в брак.
Каждая операция прописывается: что использовать, как и чем замерять результат. Например, стандарт ISO 9001 уже лет двадцать, как обязателен почти для всех крупных предприятий. И тут не обошлось без тонкостей: одним внедрить бумагу, другим – реально заставить по ней работать.
Вот как обычно выглядит набор важных документов на заводе:
- ГОСТы и ТУ (технические условия) на продукцию и материалы;
- Технологические карты на каждый участок;
- Инструкции по контролю качества для каждого этапа;
- Журналы проверки и акты выявленных дефектов;
- Сертификаты соответствия на исходное сырьё и компоненты;
- Ведомости изменения документации (если что-то модернизируется или корректируется).
Без бумажной рутины никуда, но полезно помнить: чем проще понять инструкцию, тем больше шансов, что стандарт будет соблюдён.
Контрольные точки — сердце контроля качества: по сути, это заранее определённые этапы, когда результат надо проверить особо тщательно. Вот типичные примеры таких точек:
- Входной контроль сырья;
- Промежуточная проверка после ключевых операций (например, сварка или обработка);
- Итоговый контроль готовой детали;
- Проверка упаковки и маркировки.
Исследования СНИИМ показывают, что если не пропускать ни одной контрольной точки, количество претензий снижается минимум на 40%. Это статистика с реальных машиностроительных предприятий.
Контрольная точка | Ответственный | Инструмент контроля |
---|---|---|
Входной контроль | Отдел ОТК | Сырьевые протоколы, лабораторные анализы |
Проверка после обработки | Мастер цеха | Шаблоны, измерительные приборы |
Финальный контроль | Инженер по качеству | Контрольные карты, тесты |
Без списка стандартов, чёткого плана контроля и регулярных сверок вся работа по управлению качеством пойдёт насмарку. Как пишет журнал "Металлургия и машиностроение":
«Подменять стандарты привычками рискованно. Регламент всегда побеждает „авось“, если речь про качество и деньги».
Стоит периодически пересматривать все документы: завод устаревшими инструкциями губит новые проекты чаще, чем кажется.
Популярные ошибки и как не наступать на старые грабли
В управлении качеством на заводах часто встречаются одни и те же недочёты. Их можно избежать, если знать основные ловушки. Разберёмся, что чаще всего ломает систему в машиностроении и как этого не допустить.
- Доверие только финальному контролю. Очень многие считают, что если на выходе стоит строгий контроль, всё остальное не так важно. В итоге ОТК завален браком, а потери времени и денег льются рекой. Контроль должен быть встроен в каждый этап.
- Отсутствие чётких стандартов. Когда нет внятных документов и инструкций, каждый понимает "качество" по-своему. Это всегда оборачивается конфликтами между отделами: одни уверены, что детали нормальные, другие – что пора списывать всю партию.
- Игнорирование проблем на ранней стадии. Если рабочий заметил косяк, но не сообщил, потом устранить ошибку стоит в разы дороже. Вот почему во многих топовых заводах премируют сотрудников за то, что они нашли и показали проблему, а не скрыли её.
- Слабое обучение персонала. Люди часто работают по старой памяти или учатся друг у друга не самым лучшим методам. Не жалейте времени на регулярное обучение и разбор реальных кейсов!
- Неучтённые смены условий. Любое новое оборудование, купленная сталь или смена поставщика требуют быстрой адаптации стандартов контроля качества. Прежние инструкции могут перестать работать — этим часто пренебрегают, и получают только новые проблемы.
Очень жизненный пример: на одном производстве внедрили систему ISO 9001, но забыли вовремя обновить инструкции, когда начали покупать у нового поставщика металла. Год партнёрство длилось, пока не выяснилось — свойства металла не соответствуют заданным параметрам. Всё это время система считалась рабочей, хотя контролила уже совсем не то, что нужно.
Ошибка | Средняя частота на 10 цехов |
---|---|
Проблемы из-за устаревших стандартов | 7 |
Ошибки из-за формального финального контроля | 8 |
Игнорирование сигналов от рабочих | 6 |
Запомните: настоящая система управления качеством — это процесс, а не разовый документ. Ошибки повторяются лишь там, где их игнорируют или стесняются обсуждать открыто. Чем активнее команда делится обнаруженными косяками, тем меньше утерянных денег и срывов поставок.
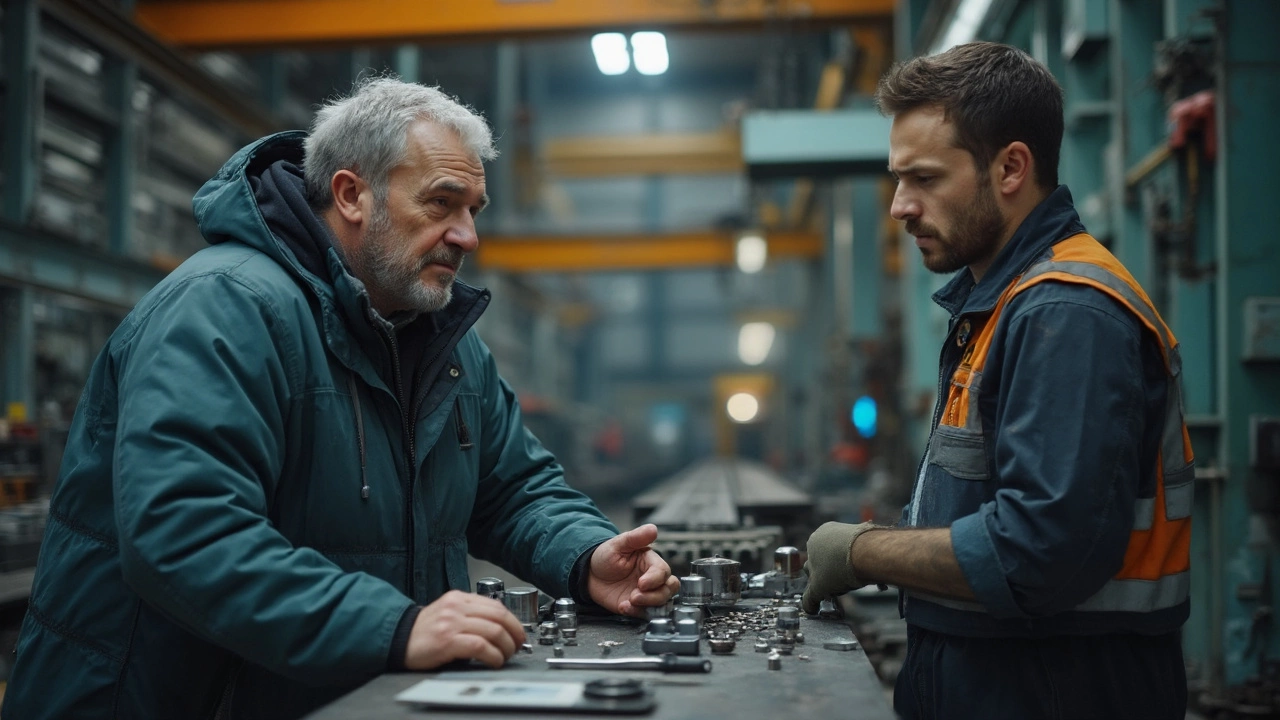
Реальные советы по повышению качества
Повышение качества в машиностроении — это не только про новые станки или строгие стандарты. Многие компании упираются в привычки и устаревшие процессы, а не в оборудование. Вот что помогает двигаться вперёд.
- Автоматизируйте проверки. Уже старый факт: при ручной проверке деталей, средний процент пропущенного брака по России колеблется около 3%. С внедрением автоматизированных систем этот процент падает почти до 0.5%. Камеры или датчики выявляют то, что устающий контролёр запросто пропустит.
- Обучайте сотрудников замечать риски. Практика одной из калужских фабрик показала: когда каждый токарь и сварщик разбирается хотя бы в основах управления качеством, количество рекламаций от клиентов упало на четверть всего за год. Проводите короткие тренинги, не гонитесь за «корочками» ради отчётности.
- Регулярно меняйте контрольные листы. Многие начинают просто листать глазами старые чек-листы и не замечают ошибок. Перерабатывайте форму контроля раз в квартал. Это простое действие помогает не пропускать новые слабые места процесса.
- Проводите разборы реальных браков, а не только пишите отчёты. Например, раз в месяц собирайте команду прямо у станка и смотрите под микроскопом, где конкретно пошёл сбой — это гораздо полезнее длинных совещаний.
- Не экономьте на контроле сырья. Если искать проблему только на финальной стадии, вы потратите в разы больше ресурсов. По данным одного производственного аудита, 60% дефектов в машиностроении заложены сырьём, а не ошибками в обработке. Простой входной контроль избавляет от массы рекламаций.
Для наглядности можете взглянуть на средние показатели по снижению брака после внедрения простых шагов на предприятиях малого и среднего машиностроения:
Мера | Среднее снижение брака |
---|---|
Автоматизация контроля | до 70% |
Обучение персонала | до 25% |
Актуализация чек-листов | до 10% |
Разбор брака на месте | до 18% |
Самое главное — не останавливаться. Контроль качества в машиностроении — это марафон, где выигрывает тот, кто меняет процессы чуть быстрее остальных.
Комментарии