Каждый раз, когда вы держите в руках новый смартфон, велосипед или даже обычную кастрюлю, вы вряд ли представляете, какой сложный путь все это проходит на производстве. Вокруг заводов всегда было много мифов — например, что всё там автоматизировано, что люди почти не нужны, или что проверить качество можно простым взглядом. На самом деле, даже в эпоху роботов и цифровых двойников, настоящие заводы — это не только цеха, полные станков. Самое интересное у них внутри — три процесса, без которых ни одно производство не взлетит: выпуск продукции, контроль качества и логистика. Вот кто реально держит все нитки в руках.
Производство как сердце любого завода
Производство — это не просто «сделать деталь». Здесь всё начинается с проектирования и закупки нужных материалов. Только представьте: на одном крупном заводе ежедневно обрабатывают тысячи тонн металла — и это только начало. Многие сейчас считают, что всю работу делают станки, но без наладки, настройки, человеческого ума и прямых рук ничего не получится. Мой знакомый работает мастером на заводе — он говорит, что иногда, чтобы понять причину сбоя на линии, простого опыта мало, приходится разбираться с деталями из нескольких цехов. Каждый участок связан с другим, и выходит настоящий живой организм, а не просто набор цехов.
Кстати, есть один интересный факт: ещё в 2013 году завод Toyota в Японии провёл эксперимент — часть операций снова начали делать вручную. Оказалось, рабочие смогли придумать улучшения, которые машине не пришли бы в голову. Поэтому даже ультрасовременные предприятия возвращают часть функций мастерству людей. Технологии шагнули далеко, и в современных цехах за одну смену могут выпускать больше продукции, чем полвека назад за месяц, но за этим всегда стоит грамотное планирование.
Производственный цикл — во многом шахматная партия. Не только детали и узлы должны быть готовы вовремя, но и сырье, комплектующие, а еще специалисты, знающие, как работать с новым оборудованием. Сейчас на передовых предприятиях заводят цифровые двойники: на компьютере «копируют» линию, просчитывают варианты до запуска. Это экономит кучу времени — меньше брака, меньше сбоев, и меньше потерь.
А еще производство — это всегда постоянные изменения. Вчера собирали один гаджет, а через неделю надо запускать новый. Здесь играют роль короткие сроки переналадки линий, автоматизация, но и старая добрая смекалка — куда без нее? Человеческий фактор никуда не делся. На практике, если даже у самого лучшего автомата сгорит контроллер, только опытный инженер местного завода за полчаса решит дело, а не специалист где-нибудь за тысячи километров.
В итоге, производство объединяет старое и новое: ручной труд, который дополняют роботы и «умные» системы контроля. Не ошибусь, если скажу: здесь борются скорость и качество, но без людей и их чувств к деталям все равно ничего не выйдет.
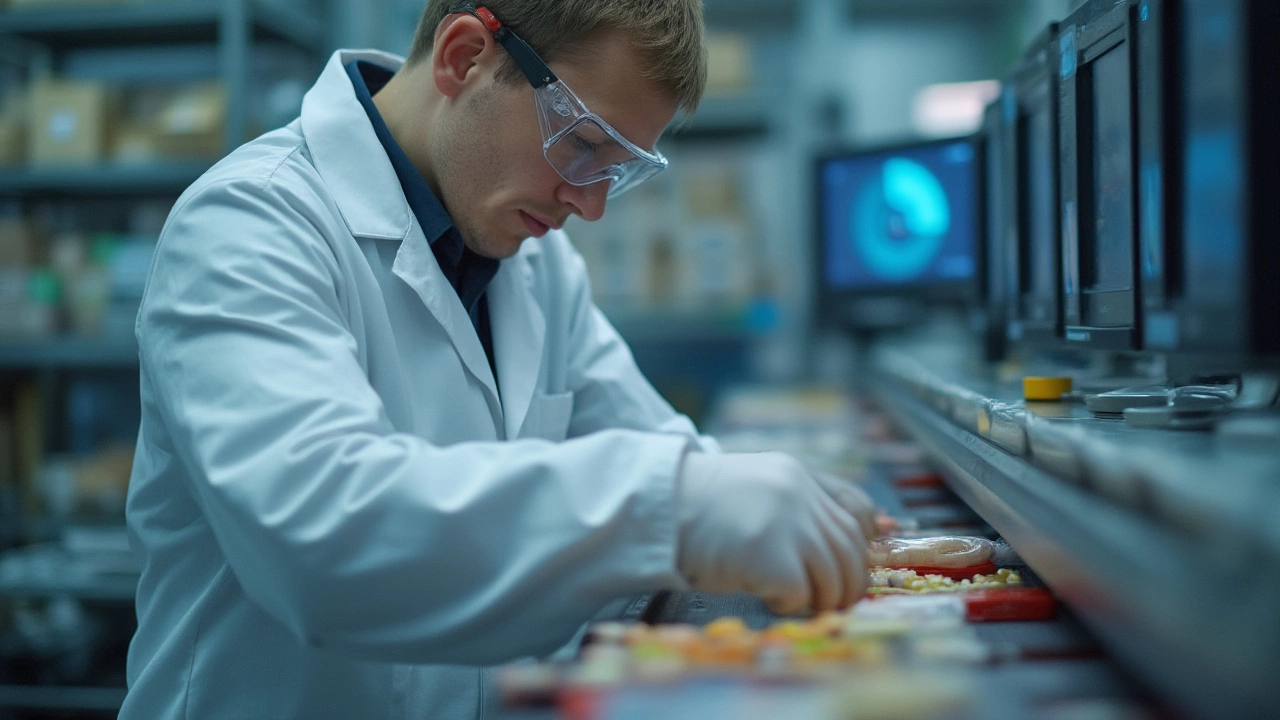
Контроль качества: барьер между браком и идеальным продуктом
Каждый раз, когда Максим (мой кот) роняет на пол кружку, я по-новому начинаю ценить надёжность вещей. Качество — это не пафосное слово. На заводе контроль качества может занимать больше времени, чем само производство. На научно-исследовательском институте в Казани проводили эксперимент: брали две партии труб — на одной был усиленный контроль качества, на другой обычный. Через год использования стало ясно: усиленный контроль позволяет снизить брак почти на 60%. Это огромная экономия для компании и спокойствие для клиентов.
Система контроля — не просто «глаз да глаз», а целая цепочка, где каждая стадия производства пропускает детали через строгий фильтр. Часто внедряют автоматические системы — например, камеры, способные за секунду обнаружить микротрещину. Но, что интересно, до сих пор на сложных участках последнюю точку ставят люди: опытный техник способен заметить то, что для компьютера выглядит нормой. Иногда в качестве эксперимента выпускают «контрольные партии» — это когда новые технологии проходят жесткую проверку задолго до массового запуска.
В принципе, современные стандарты (например, ISO-9001) требуют строгих, пошаговых систем проверки. Если завод их не соблюдает, ни одна уважающая себя компания не будет покупать его продукцию. Каждый успешный завод делает ежедневные тесты. Смешно, но есть даже свой «черный ящик» — на линиях ставят особые контейнеры для деталей, которые вызвали хоть малейшее подозрение. Дальше идет разбирательство, как в сериале.
Иногда можно услышать: «Контроль нужен только чтобы не нарваться на брак». Истина в другом: грамотная система контроля качества становится настоящей школой для всего коллектива. Мой приятель работал на производстве бытовой техники и регулярно сталкивался с ситуацией, когда грамотный совет мастера помогал улучшить продукт — чтобы он не только работал, но и «выживал» у самых рассеянных хозяев. На самом деле, государственная статистика показывает: компании, которые регулярно вкладываются в контроль качества, зарабатывают в полтора раза больше, чем те, кто экономит на этом.
Если бы спросили, что главное — скорость или качество, любой производственник ответил бы: без качества не будет ни продаж, ни репутации. Иногда даже введение простых дополнительных тестов спасает от серьёзных потерь. Например, известная история на одном европейском заводе: после автоматизации одного участка забыли учесть соседние факторы, и продукция стала выходить больше, но с браком. Вернулись к ручному двойному контролю, и проблемы исчезли. Вот он — баланс между технологиями и опытом.
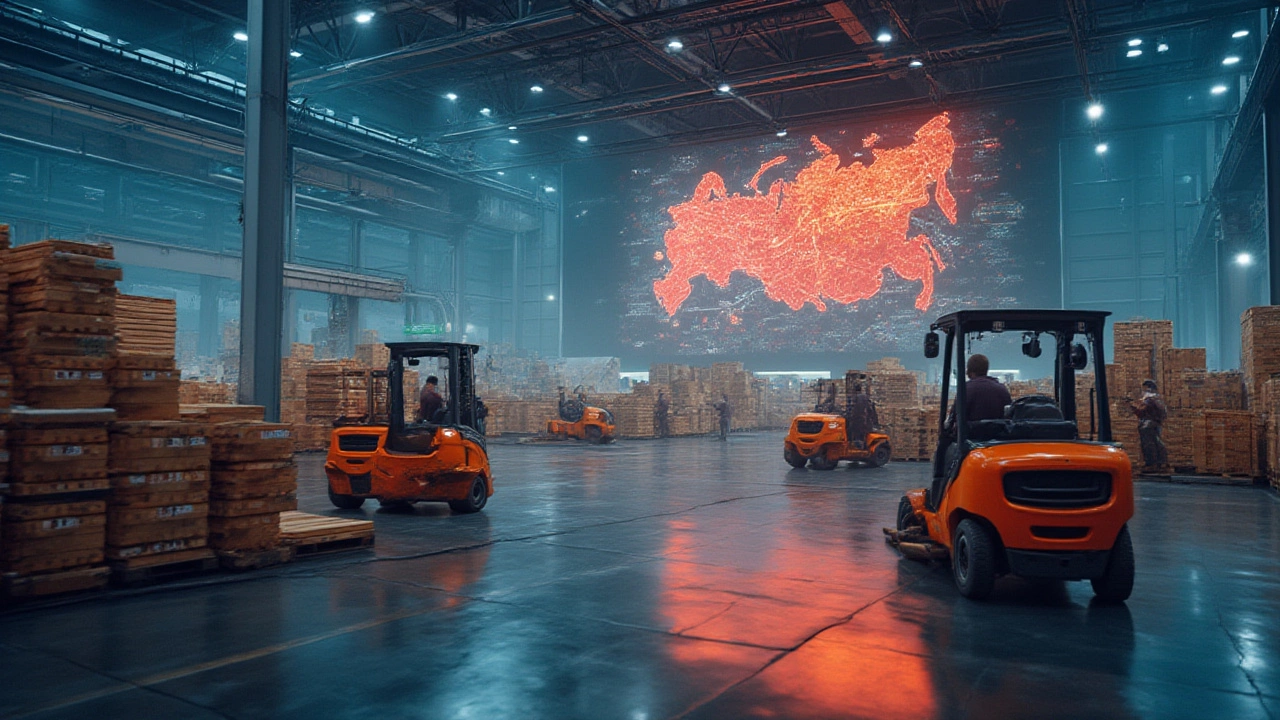
Логистика: система, которая всё связывает
Многие думают, что логистика — это только про склады и грузовики. На самом деле там свои законы — без хорошо выстроенной логистики ни одна деталь не окажется на своем месте, а готовая продукция не доедет до магазина без задержек и потерь. Можно производить хоть сто тысяч товаров в день, но если логистика подкачает, всё встанет.
Могу рассказать историю: у одного большого предприятия в Татарстане возникла настоящая проблема — на складе не хватило места, потому что не просчитали оборачиваемость материалов. В результате, новая партия не попала на линию вовремя, и цех встал почти на сутки. Разгребать пришлось долго, но проблему решили благодаря внедрению IT-системы. Специальные программы позволили автоматизировать закупки, отслеживать движение сырья в режиме реального времени и понимать, какой товар на складе и когда ждать следующую поставку.
Современная логистика уже не обходится без цифровых помощников. Например, на многих заводах стоят датчики RFID — они отслеживают любое перемещение ящика. Это помогает быстро находить нужную деталь и выстраивать маршрут без лишних переездов по территории. А ещё автоматизация позволила быстрее формировать заказы, оптимизировать работу транспорта и даже сократить простои. Без грамотной логистической схемы оборот сокращается, а расходы на хранение сырья увеличиваются в разы.
Важно помнить, что логистика — не только движение материальных ценностей. Это всё про планирование: что, где и когда должно быть, чтобы не возникло ни дефицита, ни залежавшихся партий. На крупных предприятиях логистика делится на внутреннюю (всё, что касается движения по цехам, складам, перемещения деталей) и внешнюю (то, как продукция попадает к потребителю). Каждая ошибка в логистике — это задержки, потери и лишние затраты.
В Европе среднее время отгрузки продукции с завода до склада клиента сократилось за пять лет в два раза — благодаря новым логистическим программам и автоматизации. В России к этому тоже всё чаще идут. Например, на машиностроительных заводах Казани внедряют собственные мобильные приложения для отслеживания запасов и самой отгрузки — чтобы каждый работник видел, где находится заказ, и мог быстро реагировать на любые изменения. В итоге исчезает хаос, сокращаются очереди и почти исчезают форс-мажоры.
Кстати, умная логистика помогает не только заводу — выигрывают все. Клиенты не ждут свою новую стиральную машину недели, а обычный мастер не стоит часами у рейки, проверяя, пришла ли нужная деталь. Снижается нагрузка на персонал, уходит лишняя нервотрёпка. Самое интересное, что такой подход экономит немалые деньги предприятиям: меньше простоев — больше прибыли.
Ну и нельзя забывать, что логистика — это ещё и безопасность. Хранение химических веществ, перевозка крупногабаритных станков требует чёткого учета и ответственности. Малейший сбой — и риски возрастают. Поэтому грамотная логистическая схема — такая же часть успеха предприятия, как производственная линия или система контроля качества. Если логистикой занимается неравнодушная команда — всё будет идти как по маслу.
Вместе эти три процесса — основные процессы современного производственного предприятия. Как детали одного механизма, они не работают в одиночку: стоит завести сбой в одном, и вся машина рискует остановиться. Если хочется разобраться, почему некоторые заводы идут впереди, причина тут. Мои наблюдения показывают: чем лучше построены эти процессы, тем проще всем — от слесаря до директора и клиента, который будет пользоваться вещью долгие годы.
Комментарии