Процесс управления качеством в машиностроении — это основа для обеспечения надежности и безопасности продукции. Этот процесс не стоит на месте, так как технологии и подходы постоянно развиваются, способствуя внедрению новых стандартов и методов контроля.
Одним из ключевых элементов является четкое определение стандартов качества, которые помогут в достижении требуемых характеристик продукции. Это позволяет не только удовлетворять потребности рынка, но и предвосхищать их, оставляя конкурентов позади.
Значимым этапом является и планирование процессов контроля качества. Без него невозможно создать систематический подход, который позволит вовремя выявлять недостатки и оперативно принимать меры по их устранению.
- Определение стандарта качества
- Планирование процессов контроля
- Реализация систематического подхода
- Инструменты оценки качества
- Анализ и исправление ошибок
- Постоянное улучшение процессов
Определение стандарта качества
Важность определения стандарта качества в машиностроении нельзя переоценить. В современных условиях жесткой конкуренции и стремительно развивающихся технологий, стандарт качества — это не просто набор требований, а стратегический инструмент, позволяющий оставаться на плаву и добиваться успеха. В первую очередь, это понимание того, каким образом конкретный продукт должен соответствовать ожиданиям как самого производителя, так и конечного пользователя. Стандарт качества начинают формировать на стадии разработки продукта, и он влияет на весь цикл его создания — от проектирования до конечных тестов. Особое значение имеют такие аспекты, как долговечность, безопасность и функциональность. Для их достижения предприятия тщательно анализируют рыночные потребности и запросы клиентов.
Зачастую стандарты качества устанавливаются на основе международных норм, таких как ISO, которые предоставляют подробные указания по различным аспектам управления качеством. Существуют и отраслевые стандарты, разработанные с учетом специфики конкретных производств. Например, в автомобилестроении активно используется стандарт ISO/TS 16949. На этапе определения стандарта все детали изготавливаемых узлов, а также процесс их производства, оцениваются на соответствие заданным требованиям.
По словам Питера Сэнди, эксперта в области управления качеством, "качество начинается с понимания того, что нужно потребителю, и заканчивается тем, как удовлетворить эту потребность наилучшим образом".Таким образом, определение стандарта качества — это не только технический вопрос, но и способ диалога с клиентами, направленный на постоянное улучшение их удовлетворенности.
Помимо международных стандартов, крупные компании часто разрабатывают свои собственные руководства по качеству, основываясь на многолетнем опыте и лучших практиках. Понимание своих процессов и тщательный мониторинг каждого этапа производства помогают добиваться неизменно высокого уровня исполнения. Другой важный аспект — это подготовка квалифицированного персонала, который сможет не только соблюдать установленные нормы, но и предлагать решения для оптимизации процессов. В связи с этим, обучение и культура качества на всех уровнях компании становятся краеугольным камнем в цепочке создания ценности. Организация регулярных тренингов и курсов повышает осведомленность сотрудников о последних тенденциях и новациях в области качества.
Интерес представляет также статистика: компании, внедрившие стандарты качества, значительно снижают риск дефектов на выходе. Это подтверждается исследованиями, которые показывают, что предприятия, уделяющие внимание процессам контроля качества, сталкиваются с жалобами клиентов намного реже.
Фактор | Компании с ISO | Компании без ISO |
---|---|---|
Уровень жалоб | 2% | 15% |
Качество продукции | 98% | 85% |
Планирование процессов контроля
Планирование процессов контроля представляет собой фундаментальную стадию в системе управления качеством в машиностроение. Оно начинается с детального анализа требуемых характеристик продукции и формулировки конкретных целей качества. Эти цели должны быть реалистичными, измеримыми и соответствовать международным стандартам. На этом этапе важно учитывать специфические условия производства и особенности используемых материалов.
Процесс планирования также включает разработку контрольных мероприятий, которые будут применяться на различных стадиях производственного цикла. Это могут быть как традиционные методы, такие как визуальная проверка готовых изделий, так и современные подходы, включая автоматизированные системы контроля с использованием компьютерных технологий. Важно выбрать такие методы, которые наиболее эффективно справляются с поставленными задачами.
Организация взаимодействия между отделами производства и контроля качества также является ключевым аспектом. Это помогает создавать единые стандарты и избегать недопонимания. Взаимодействие должно быть налажено так, чтобы любые отклонения от заданных стандартов были обнаружены как можно раньше, и были предприняты меры по их исправлению.
"Качество — это соответствие требованиям клиента" — так говорил Эдвард деминг, основатель системы тотального управления качеством. Его подходы и до сих пор актуальны в современном машиностроении.
Не следует забывать и о тренингах и обучении сотрудников. Ведь без грамотного персонала даже самые современные технологии могут оказаться неэффективными. Регулярные курсы повышения квалификации и ознакомление с последними подходами к контролю качества играют огромную роль в успешной работе производства.
Таким образом, качественно выполненное планирование процессов контроля способствует не только увеличению надежности и долговечности продукции, но и повышению общей конкурентоспособности компании на рынке. Успешный опыт показывает, что компании, которые уделяют должное внимание этому этапу, могут существенно снизить производственные издержки и улучшить репутацию среди клиентов.
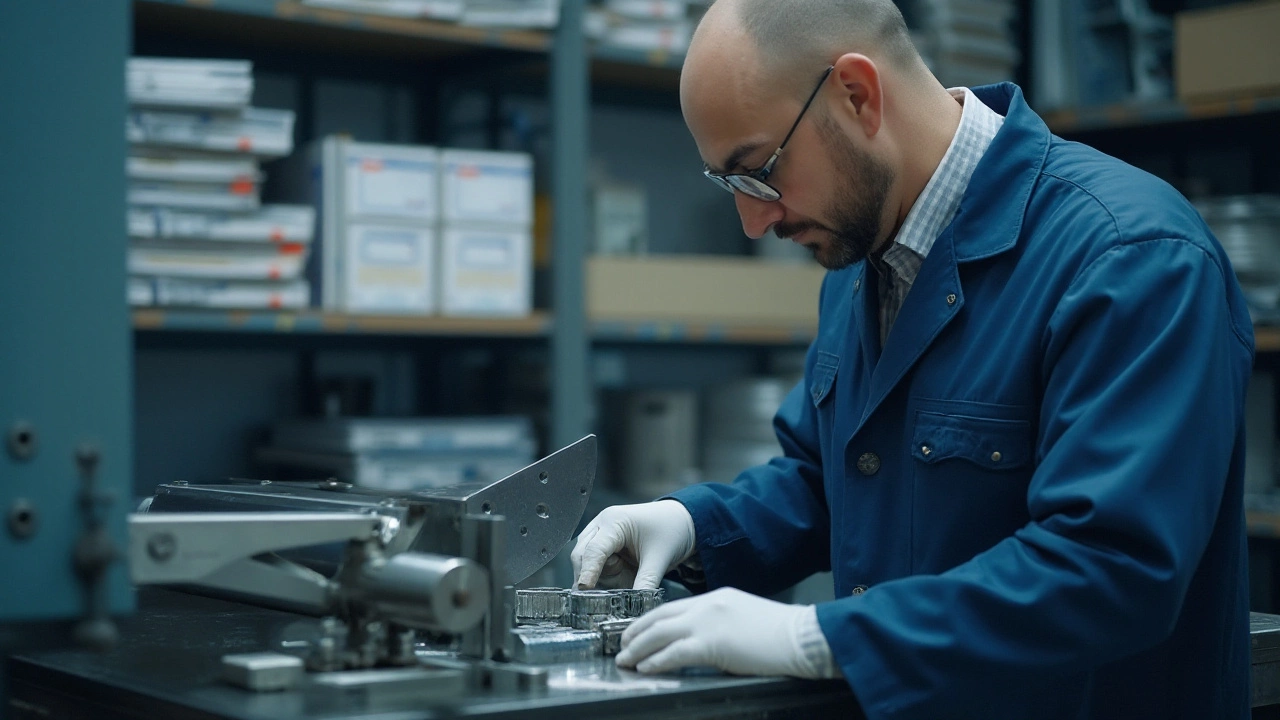
Реализация систематического подхода
Систематический подход к управлению качеством в машиностроении начинается с внедрения организованных процессов и структур. Это означает создание структуры, в которой каждый сотрудник понимает свою роль и ответственность. Такой подход позволяет создать комплексную сеть, где все элементы работают на создание продукта высокого качества. Важно подчеркнуть, что без специально наладженной системы контроля, обнаружение и устранение дефектов может занять слишком много времени, что негативно скажется на производственном процессе в целом.
В машиностроении часто привлекаются методы, которые задействуют науку о данных. Например, собирается информация в каждой стадии производства для последующего анализа и модернизации процессов. Это позволяет выявлять закономерности и пробелы, которые можно исправить. Такой подход не только повышает стандарты качества, но и позволяет сэкономить ресурсы и экономические расходы компаний на более долгосрочной перспективе.
Стандарты качества - неотъемлемая часть систематического подхода. Они могут включать как внутренние требования компании, так и соответствие международным ихериях. Команда инженеров и специалистов по качеству часто использует международные стандарты, такие как ISO, как эталон для своих проверок. Это устраняет несоответствия и обеспечивает, что конечный продукт будет соответствовать ожиданиям пользователей. Повышение осведомленности команд о важности контроля качества через семинары и тренинги также играет существенную роль в реализации систематического подхода.
"Качество никогда не бывает случайным, это всегда результат целенаправленных усилий." — Джон Рашкин
Для реализации систематического подхода важно обеспечить поддержку на всех уровнях организации. Это значит, что руководство должно активно вовлекаться, давать необходимые ресурсы и поддержку командам, исполняющим программы контроля качества. возможность завести обратную связь также ключевое условие успеха. Открытый диалог между инженерами, менеджерами и производственными рабочими способствует созданию культуры качества, где выявление и предотвращение дефектов становится приоритетом для всех.
И как показывает практика, еще одним эффективным способом достижения высокого уровня качества является применение методов всеобщего качества (TQM). Это процесс, который подразумевает всеобщую вовлеченность сотрудников в улучшение качества выпускаемой продукции, что снижает вероятность ошибок и значительно повышает уровень удовлетворенности клиентов. Это не только создает позитивный настрой внутри коллектива, но и демонстрирует стремление компании к совершенству. Подход TQM также создает конкурентное преимущество на рынке, помогая привлечь новых клиентов и удержать существующих.
Инструменты оценки качества
Оценка качества продукции — важный этап в машиностроении. На этом этапе применяются различные инструменты оценки качества, которые позволяют получить объективные данные о характеристиках продукта. Один из самых распространенных инструментов — это статистический контроль. Он эффективно помогает в идентификации возникающих отклонений от нормы. Такие инструменты помогают следить за стабильностью и качеством производственных процессов, предпринимая корректирующие меры вовремя.
Кроме статистического контроля, широко применяются и методы визуального контроля. Этот метод основан на проверке продукции визуально на наличие дефектов. Несмотря на кажущуюся простоту, он является важной ступенью грубой фильтрации несоответствий до детальной проверки. Часто используют и неразрушающие методы контроля, такие как ультразвуковая и рентгеноскопическая диагностика, которые активно применяются для обнаружения скрытых дефектов внутри деталей.
Эффективное использование инструментов оценки напрямую зависит от квалификации сотрудников. Обретение навыков применения различных методов анализа и контроля играет не последнюю роль. Некоторые компании проводят регулярные тренинги и аттестации для повышения уровня профессионализма рабочих. Высококвалифицированный персонал способен быстро и точно определять не только очевидные, но и скрытые недостатки, минимизируя при этом вероятность их дальнейшего влияния на конечный продукт.
"Качество — это когда продукция соответствует или перевыполняет ожидания клиента", — говорил Эдвардс Деминг, основатель философии постоянного улучшения.
Современные технологии способствуют развитию новых подходов к обеспечению качества. В последнее время получают популярность автоматизированные системы контроля качества, интегрированные с машинами и производственными линиями, что позволяет значительно сократить время на проверку и улучшить точность измерений. Это открывает новые возможности для производств: позволяет снизить затраты и повысить конкурентоспособность на рынке.
- Визуальный контроль: позволяет быстро выявить дефекты на поверхности.
- Неразрушающие методы: выявляют скрытые дефекты внутри материала.
- Статистический контроль: идентифицирует отклонения в производственных процессах.
Для внедрения качественного контроля важно правильно организовать работу систем оценки, обеспечивать регулярное обновление методик и обучение сотрудников, что будет формировать культуру качества на предприятии и повышать эффективновость управления.

Анализ и исправление ошибок
Анализ и исправление ошибок в процессе управления качеством – это одна из главных задач, стоящих перед инженерами и специалистами по производству в сфере машиностроения. Ошибки ни в коем случае нельзя оставлять без внимания, так как каждая из них может привести к снижению качества продукции или даже более серьезным последствиям, таким как поломка оборудования или несчастные случаи. Чтобы предотвратить такие инциденты, необходимо разработать четкую стратегию анализа и исправления ошибок, которая будет учитывать не только устранение самих дефектов, но и их причин.
Первым шагом в любом эффективном процессе анализа является выявление ошибки. Это включает в себя использование различных методов и инструментов, таких как статистический анализ и методы FMEA (Анализ видов и последствий отказов). Эти инструменты помогают тщательно изучить каждый аспект производственного процесса, начиная с материала и заканчивая финальной стадией сборки. Успешное выявление ошибок позволит устранить их на ранней стадии, что минимизирует издержки и предотвращает их повторное появление.
Один из ключевых элементов исправления ошибок — вовлечение специалистов на всех уровнях производства. Это важно, потому что ошибки могут происходить на любом этапе и участие тех, кто непосредственно участвует в создании продукции, часто бывает решающим. Важно, чтобы каждый член команды имел возможность открыто высказываться о проблемах и предлагать решения. Такой подход помогает сформировать атмосферу доверия и упрощает диагностику проблем.
"Ошибки следует исправлять не потому, что они выявлены, а чтобы они больше не повторялись" – известный совет экспертов по контролю качества.
Исправление ошибок требует детального плана, который должен содержать конкретные шаги по устранению дефекта и предотвращению его в будущем. На этом этапе также важно задокументировать весь процесс, чтобы наглядно видеть, где произошел сбой и что было сделано для его устранения. Кроме того, это помогает обучать персонал, предоставляя им конкретные примеры и уроки из реальных ситуаций.
Также для полноценного решения необходимо внедрение новых технологий контроля и улучшение существующих методик. Современные системы автоматизации могут значительно упростить и ускорить процесс выявления и исправления ошибок, автоматически отслеживая производственные данные и сигнализируя о возможных отклонениях от норм. Совмещение таких технологий с квалифицированной работой специалистов создаёт мощный инструмент для изучения и повышения качества продукции, который позволяет оставаться конкурентоспособными на насыщенном рынке. И наконец, одним из важных аспектов является постоянное улучшение процессов на основе анализа ошибок. Это часть философии управления качеством, которая требует непрерывного совершенствования и адаптации к изменяющимся условиям. Чем ближе внимание уделяется возникновению и устранению ошибок, тем более надежной и качественной становится продукция.
Постоянное улучшение процессов
В современном машиностроении постоянное улучшение процессов становится неотъемлемой частью мощного инструмента для достижения высокой конкурентоспособности. Это включает в себя не просто исправление ошибок, но и предвосхищение будущих изменений, чтобы производственные системы оставались на пике эффективности и надежности. Улучшение процессов подразумевает модификацию существующих методик и создание новых стратегий, которые могут улучшить производительность, снизив при этом количество отходов и затрат.
Ключевая аспекта постоянного улучшения заключается в применении подхода Kaizen, который фокусируется на ежедневных небольших улучшениях, в отличие от крупных и радикальных перемен. Эффективное управление качеством помогает компаниям сосредотачиваться на непрерывном совершенствовании, что в свою очередь позволяет им минимизировать дефекты и улучшать производственный цикл. Это не только о повышении качества продукции, но также и об обучении сотрудников, что еще более значимо в корпоративной культуре.
Часто организации применяют методики Lean и Six Sigma для усиления своих стратегий улучшения качества. Это сочетание позволяет оптимизировать каждый процесс таким образом, чтобы свести к минимуму потери ресурсов. Инструменты оценки качества, такие как диаграммы причинно-следственных связей и контрольные карты, помогают понимать, где имеются узкие моменты и как их можно исправить.
"Качество — это не просто соблюдение стандартов. Это путь, ведущий к оптимизации и совершенствованию всех аспектов производства." — Деминг
Тем не менее, добиться непрерывного улучшения невозможно без эффективной системы обратной связи, где сотрудники, клиенты и поставщики активно участвуют в процессе, предлагая свои идеи и решения. Это требует высокой степени вовлеченности и доверия. Непрерывное улучшение становится образом мышления как для руководителей, так и для рабочих на всех уровнях организации, создавая атмосферу инновационных изменений.
Методы | Цель |
---|---|
Лин Производство | Снижение потерь |
Шесть Сигм | Устранение дефектов |
Работа с данными и анализ показателей также являются неотъемлемой частью постоянного улучшения. Продвинутые системы мониторинга позволяют компаниям вовремя замечать отклонения от норм, делая каждое изменение предсказуемым и управляемым. Использование этих данных для корректировки и усовершенствования производственных методов является ключом к укреплению позиций на рынке и индустрии.
А кто лучше всего может рассказать о важности даного процесса, как не сама конкуренция? В условиях современного мира, где высокие технологии и изменения происходят стремительно, именно постоянное улучшение процессов способно не только догонять, но и опережать другие компании. Это не просто шаг вперед — это обязательная прерогатива для любого, кто стремится быть лидером в своей области.
Комментарии