3D-моделирование в машиностроении – это сложный процесс, включающий в себя несколько важных этапов. Каждый шаг здесь имеет свою значимость, и третий этап особенно примечателен. Именно на этой стадии проект обретает свою реальную функциональность, когда анализирует каждую деталь в условиях близких к реальным. Инженеры используют различные техники для оценки того, как себя поведёт финальный продукт. Изучим детальнее, что же подразумевается под третьим этапом в 3D-моделировании и как передовые технологии облегчают этот процесс.
- Определение третьего этапа
- Роль CAE в инженерии
- Типичные процедуры на этапе анализа
- Софт для 3D-анализов
- Практические советы и хитрости
Определение третьего этапа
Третий этап в 3D-моделировании играет ключевую роль в проектировании и разработке современных конструкций в машиностроении. На этом этапе осуществляется глубокий анализ с использованием методов вычислительной инженерии, таких как CAE (Computer-Aided Engineering). Этот процесс включает в себя симуляцию и тестирование под воздействием реальных условий эксплуатации, таких как температурные изменения, механические нагрузки и другие факторы окружающей среды. Идея заключается в том, чтобы заранее предсказать поведение изделия и подготовить его к реальным испытаниям.
Важность третьего этапа нельзя недооценивать, поскольку здесь инженеры могут выявить слабые места продукта и провести оптимизацию конструкции. Обычно в рамках CAE применяются такие методы, как метод конечных элементов (FEM) и динамический анализ, что позволяет разбирать различные аспекты функциональности конструкции. Данные о таких аспектах, как напряжение и деформация, можно получить ещё на стадии проектирования, что значительно сокращает время на тестирование прототипов и снижает затраты на этапах финального производства.
"Эффективный анализ на ранних стадиях проектирования способен значительно снизить ущерб от поломок и отказов оборудования," — утверждает доктор Мария Иванова, ведущий специалист CAE-аналитиков в компании 'Инноватионс-Инжиниринг'.
Для инженерных команд важно иметь не только подходящие программные инструменты, но и навыки для правильного использования данных. В текущих реалиях автоматизация играет всё большую роль. Программное обеспечение для анализа, такое как Ansys или SolidWorks Simulation, позволяет проводить всесторонние симуляции без необходимости создания физического прототипа. Эти системы предоставляют мощные алгоритмы, позволяющие заметно ускорять процесс тестирования и совершенствования изделий.
Процесс | Значение |
---|---|
Метод конечных элементов | Анализ прочности и деформации |
Динамическое моделирование | Оценка поведения при движении |
Тепловой анализ | Анализ температурных воздействий |
Развитие этих технологий привело к снижению потребности в многочисленных испытаниях на физической поверхности, что, в свою очередь, уменьшает потребление ресурсов. Экологичность и экономичность — одни из важнейших преимуществ, которые даёт нам инновационное CAE в современном машиностроении. Это не только ускоряет процесс вывода продукта на рынок, но и обеспечивает его конкурентоспособность за счёт высокого качества и надёжности.
Роль CAE в инженерии
Компьютерное вспомогательное проектирование и инженерия, или CAE, сопровождает все этапы разработки в современном машиностроении. На третьем этапе 3D-моделирования его значение становится критически важным, так как подобные инструменты позволяют буквально заглянуть в будущее, предсказывая, как проектируемые механизмы будут функционировать в реальных условиях. CAE-технологии внедряются для моделирования различных физических свойств: от механической прочности материалов до термических нагрузок, что делает возможным проведение анализа без необходимости создания физических прототипов. Это не просто удобство, а значительное сокращение временных и финансовых затрат.
Используя CAE, инженеры могут анализировать и оптимизировать свои проекты на самых начальных стадиях. Например, в случае автомобильных компонентов, CAE помогает разработчикам учитывать такие факторы, как аэродинамика и устойчивость материалов к различным условиям окружающей среды. Благодаря этому продукт выходит на рынок, пройдя тщательную проверку и без необходимости дополнительных затрат на исправление недостатков. К числу популярных программных решений для CAE относятся такие инструменты, как ANSYS, Abaqus и COMSOL, которые позволяют проводить сложные вычислительные эксперименты.
Практическое применение CAE
Основой моделирования, интеграции CAE, являются сценарии, максимально приближенные к реальной жизни. Представьте себе испытание машины на дороге: с помощью CAE возможно имитировать подобные условия, не покидая стен лаборатории. Это дает преимущество в тестировании, которое может предсказать износ деталей, необходимость улучшения определенных элементов конструкции и даже выявить потенциальные угрозы. Использование CAE позволяет проводить безопасные и исправные по стандартам проверки, которые минимизируют ошибки на ранних этапах.Интересно, что исследование, проведенное Американским обществом инженеров (ASME), показало, что компании, активно использующие CAE, сокращают время выхода на рынок новых продуктов на целых 30%.
«CAE не просто инструмент, а возможность менять мир вокруг нас, аккумулируя инженерные достижения на пороге реальности», – утверждает доктор Джон Миллер, эксперт в области компьютерного моделирования и симуляции.Каждый инженер подтверждает, что вовлеченность CAE в процесс конструирования открывает новые горизонты не только в прогнозировании, но и в креативных подходах к созданию инновационных решений.
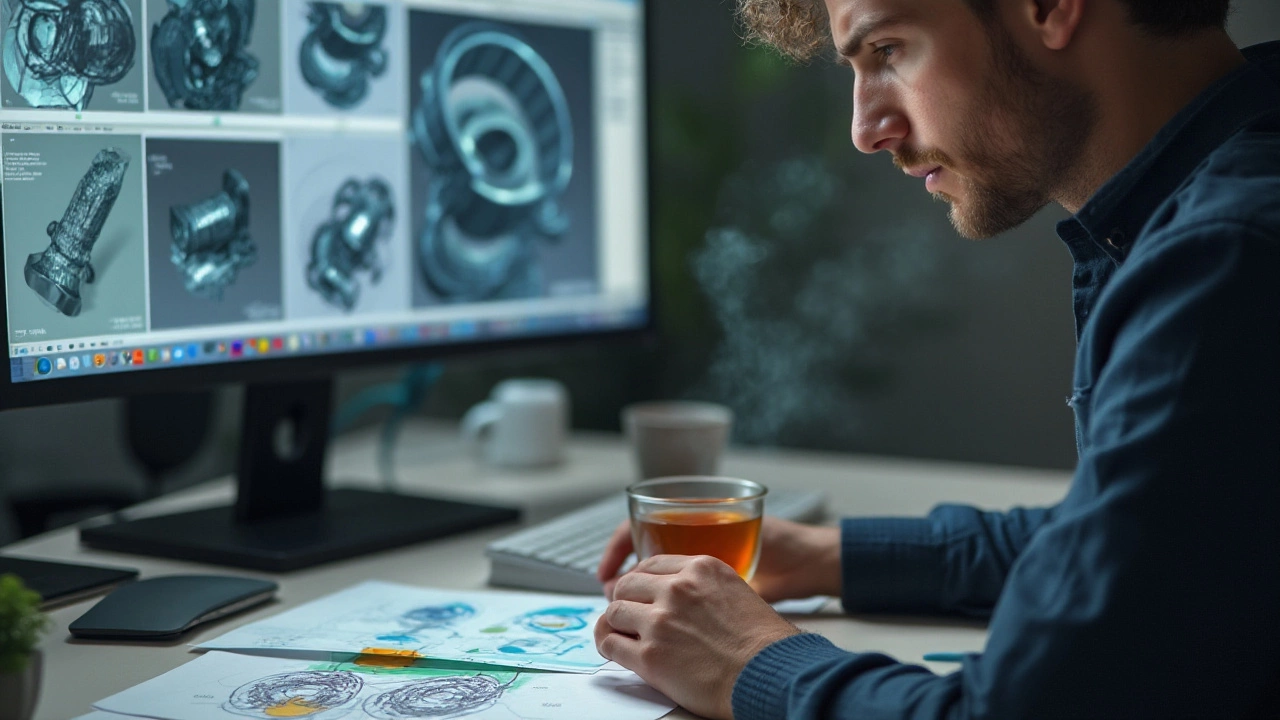
Типичные процедуры на этапе анализа
Третий этап в процессе 3D-моделирования в машиностроении характеризуется тем, что здесь проводится комплексный анализ моделей, созданных на предыдущих стадиях. Это тот момент, когда 3D-модели проходят серию детальных тестов и проверок. Эти проверки включают расчёты на прочность, анализ тепловых нагрузок и сопротивляемость различным окружающим условиям. Важно, чтобы все дефекты и недочёты были выявлены на этом этапе, так как это помогает избежать больших расходов в дальнейшей разработке или производстве. Инженеры используют многочисленные CAE-инструменты для того, чтобы моделировать данные по поведению продукта в реальных условиях эксплуатации.
Как правило, процедуры анализа включают сначала статический анализ, где проверяется, насколько модель выдерживает постоянные нагрузки при разных условиях. Далее проводится динамический анализ, симулирующий воздействия переменных факторов, таких как вибрация и колебания. Одной из важных частей этой стадии является тепловой анализ, где условия различных температурных режимов проверяются на всех уровнях конструкции. Это особенно актуально для двигателей и иных технологически сложных изделий, где перегрев может стать причиной аварии.
"Оптимизация на этапе анализа позволяет улучшить проект почти на 70%, учитывая моделирование возможных факторов. Усовершенствования, найденные на этом шаге, вносят значительный вклад в успешное внедрение конечного продукта," — говорит Альберт Смирнов, ведущий инженер компании ИТМО.
Современные технологии анализа предоставляют возможность визуализировать динамику поведения моделей в различных ситуациях. Для этого действительно требуются специальные программы, которые могут создавать наглядные симуляции. Программы, такие как ANSYS и Autodesk Simulation, распространены среди инженеров, позволяя проверять модели с высокой точностью. Внедрение подобных средств в рабочие процессы значительно улучшает качество результатов, благодаря чему конечный продукт может быть выпущен в производство с минимальными изменениями и отклонениями от начальной разработки.
- Для оптимизации процесса анализа, необходимо предугадать и учесть все возможные нагрузки на изделие.
- Каждая модель должна проходить тщательное тестирование не только на прочность, но и на устойчивость к внешним факторам, таким как влажность и температурные изменения.
- Регулярное обновление программного обеспечения помогает оставаться на острие технологий и использовать последние функции анализа.
Важно помнить, что все эти тестирования и симуляции должны проводиться в строгом соответствии с нормативными стандартами, соответствующими как международным, так и локальным требованиям. Безопасность и надежность продукта в конечном итоге зависят от точности этих проверок. Занимаясь моделированием, нельзя забывать, что от качественно выполненной работы на этом этапе зависит успех всей проектной линии, а значит и возможность сохранить высокие оценки клиентов после выхода продукта на рынок.
Софт для 3D-анализов
Из множества програмных продуктов, которые популярны в 3D-моделировании, несколько приложений стали неотъемлемой частью работы инженеров. Самым известным из них, безусловно, является ANSYS, который позволяет проводить сложные компьютерные расчёты от механической прочности до тепловых анализов. Этот софт становится особенно важным на третьем этапе моделирования, когда от характеристик отдельных деталей зависит общий успех проекта. ANSYS предоставляет возможность моделирования различных условий и гибкую настройку параметров, что позволяет инженерам предвидеть и устранять потенциальные проблемы ещё до производства изделия.
Наряду с ANSYS, нельзя обойти вниманием и SolidWorks Simulation. Эта программа особенно популярна среди разрабатываемых машиностроительных проектов из-за своей многофункциональности и интеграции с CAD-системами. С её помощью можно с лёгкостью проводить тесты на устойчивость к нагрузкам, а также учитывать термические и динамические изменения. Кроме того, SolidWorks предлагает уникальные функции оптимизации проектируемых форм и материалов, это позволяет сократить расходы и улучшить качество производства.
Важным аспектом при выборе инструмента для 3D-анализов является возможность работы в команде. Здесь на помощь приходит Altair HyperWorks, содержащий в себе модуль HyperMesh, что помогает распределённым командам работать над общими проектами благодаря мощным функциям сетевого моделирования. Эта инструментальная платформа не только облегчает процесс взаимодействия, но и позволяет улучшать точность моделирования, что модифицирует привычный подход к проектированию сложных машиностроительных конструкций.
По словам экспертов Altair, "использование каждого продукта в линейке HyperWorks может снизить затраты на проектирование до 40%".
Помимо вышеозначенных программ, Siemens NX является ещё одной мощной платформой для 3D-моделирования и CAE-анализа, особенно полезной для комплексных индустриальных проектов. Её сильной стороной считается высокая точность и скорость обработки огромного количества данных, что критично при работе с проектами в машиностроительных отраслях. Siemens NX имеет интуитивно понятный интерфейс и гибкость в настройках симуляции, что важно для инженеров, стремящихся к максимальной детализации моделей.
Имея в арсенале такие мощные инструменты, инженеры получают возможность создавать детализированные трёхмерные модели, успешно симулировать различные условия эксплуатации и понимать потенциальные силы, действующие на будущую продукцию. Стоит отметить, что грамотный выбор программного обеспечения и постоянная работа с его инструментарием позволяет значительно повысить качество конечного изделия и оптимизировать ресурсы на этапе проектирования. Такое внимание к деталям иногда позволяет инженерам открывать неочевидные аспекты и свойства поддерживающих технологий, которые могут переломить ход проектирования в ту или иную сторону.
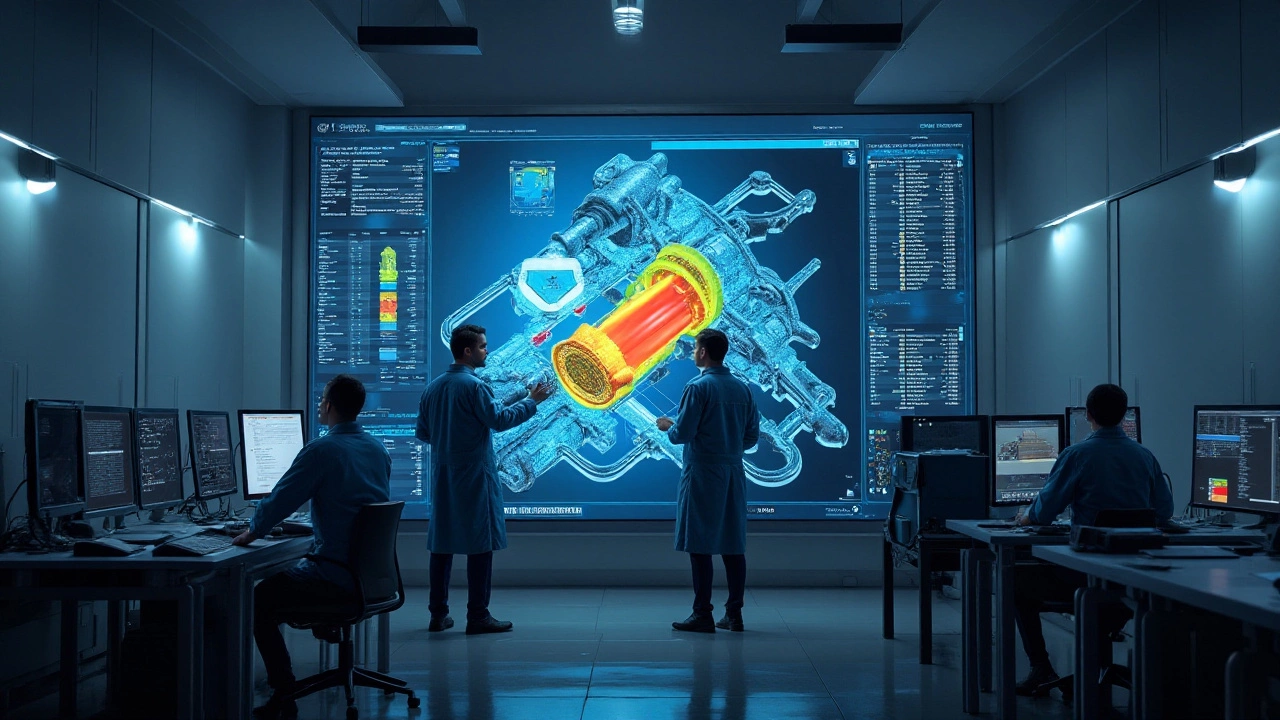
Практические советы и хитрости
Третий этап в 3D-моделировании требует не только технических знаний, но и определённых навыков, которые могут быть полезны в процессе работы. Один из ключевых моментов – понять, как среда CAE (Computer-Aided Engineering) может быть использована для имитации реальных условий. Для достижения наиболее достоверных результатов важно учитывать материал, из которого будет изготовлена деталь, а также условия её эксплуатации. Это зачастую продиктовано опытом и интуицией инженера, но технологии могут значительно упростить этот процесс.
Иммерсионное моделирование – один из таких методов, где можно прокручивать сценарии воздействия различных факторов, таких как температурные изменения или механические нагрузки. Специалисты рекомендуют начинать моделирование с упрощённой версии продукта, чтобы тестировать его поведение при изменении параметров. Таким образом, легко отследить, где может произойти ошибка или сбой. Как сказал известный инженер Генри Петров, "Моделирование – это творческий процесс, в котором главное понять, что идёт не так, как ожидалось."
"Сложность не должна быть барьером, она должна стать инструментом для достижения простоты", — отмечал Константин Иванов, специалист по CAE-технологиям.
Полезным инструментом является и цветовое кодирование результатов моделирования, когда разные цвета отображают различные области напряженности и возможные слабые места деталей. Базируясь на этих данных, инженер может сделать выводы и внести корректировки на ранних стадиях проектирования, что позволяет сэкономить время и избежать дорогостоящих ошибок на стадии производства.
Что касается использования программного обеспечения, не стоит бояться автоматизированных средств, таких как скрипты и макросы, которые могут значительно ускорить процесс обработки данных. Такой подход позволит быстрее создать проработанный продукт, минимизируя трудоёмкие рутинные задачи. Для успешной реализации всех этих советов обучайтесь новым технологиям и следите за последними разработками в области 3D-моделирования и машиностроения. Прогресс не стоит на месте, и быть его частью – значит улучшать свои проекты день ото дня.
Для более визуального подхода к оптимизации работы можно обратиться к статистике. Согласно последним исследованиям, использование CAE инструментов снижает затраты времени на разработку на 30%-40%, а затраты на материальные испытания до 50%. Это убеждает, что инвестирование в такие технологии оправдано и необходимо для эффективной работы.
Комментарии