Контроль качества в машиностроении стал неотъемлемой частью производственного процесса, позволяя обеспечить надежность и соответствие продукции установленным стандартам. Современные методы контроля качества позволяют не только находить дефекты, но и предотвращать их появление, минимизируя отходы и повышая эффективность производства.
В этой статье мы рассмотрим основные виды контроля качества, применяемые в машиностроении. Мы затронем как традиционные методы, такие как визуальная инспекция, так и современные технологии, например, автоматизированные системы и статистический контроль процессов. Знание этих методов позволит вам лучше понять, как современные предприятия поддерживают высокие стандарты качества и какие инструменты они используют для достижения этой цели.
- Традиционные методы контроля
- Современные технологии и оборудование
- Преимущества и ограничения каждого метода
- Роль автоматизации
- Статистический процесс контроль (SPC)
- Внедрение и обучение персонала
Традиционные методы контроля
Контроль качества в машиностроении изначально базировался на традиционных методах, которые служат основой даже в современных условиях. Эти методы не только прошли проверку временем, но и остаются актуальными благодаря своей простоте и эффективности. Одним из самых распространенных видов является визуальная инспекция, при которой опытные сотрудники проверяют детали и сборки на наличие видимых дефектов. Несмотря на развитие технологий, данный метод незаменим на стадии начального контроля, когда важно быстро выявить существенные дефекты, который можно заметить невооруженным глазом.
Еще одним важным элементом традиционного контроля качества является измерение размеров и соответствие этим размерам установленным стандартам. Этот подход включает использование таких инструментов, как штангенциркуль, микрометр и другие специализированные измерительные устройства. Ручное измерение позволяет оценить каждую деталь индивидуально, обеспечивая необходимую точность. Сложно представить современное производство, которое бы обошлось без этих основополагающих подходов. Исследования подтверждают, что даже минимальная ошибка в измерениях может привести к существенным проблемам на последующих этапах сборочного процесса.
Необходимо упомянуть и о механических испытаниях, которые служат важным дополнением к визуальным и измерительным проверкам. Здесь стремятся проверить надежность и прочность деталей при различных условиях эксплуатации. Предприятия проводят испытания на растяжение, сжатие и изгиб, чтобы убедиться в том, что произведенная продукция выдержит заявленные эксплуатационные нагрузки. Машиностроение требует высоких стандартов надежности, и такие методы помогают их поддерживать. Исследования показали, что продукция, прошедшая механические испытания, в 30% случаев демонстрирует повышенную долговечность.
В некоторых случаях предприятия используют и такие методы как химический анализ, чтобы удостовериться в составе материалов, которые применяются в производстве. Это особенно важно, если речь идет о производстве сложных узлов, где необходим строго определенный состав, чтобы обеспечить долговечность и соответствие требованиями. Один уважаемый эксперт в области материаловедения однажды заметил:
"Контроль состава материала является основой для создания надежной и качественной продукции в машиностроении". Такие методы, несмотря на развитие технологий, остаются важными, так как они закладывают основу для высоких стандартов качества, которые поддерживаются на всех этапах производства.
Современные технологии и оборудование
Современные технологии в области контроля качества на предприятиях машиностроения представляют собой сочетание инновационных методов и высокотехнологичного оборудования. Эти решения позволяют повысить точность и скорость проверки, устраняя необходимость в больших временных и человеческих ресурсах. Автоматизированные системы контроля качества часто интегрируются в производственные линии, где они способны проводить мониторинг в реальном времени, анализируя размерные, механические и физические параметры изготавливаемых деталей. Например, системы оптического сканирования невероятно эффективны в обнаружении мельчайших дефектов поверхности. Сенсоры такого рода способны с точностью до микрометра выявлять отклонения от допусков, что минимизирует вероятность брака.
Использование роботизированных систем все больше получает распространение в машиностроении. Такие системы не только повышают производительность, но и снижают влияние человеческого фактора, который может вызвать ошибки при визуальном осмотре. По данным исследования Ассоциации инженеров-механиков, в 2023 году до 60% крупных промышленных предприятий внедрили роботизированные решения для контроля качества на различных этапах производственного процесса. Эти роботы оснащены программным обеспечением, которое способно самообучаться, что значительно повышает их эффективность и адаптивность к новым задачам.
Неразрушающая проверка
Еще один современный метод контроля — это использование неразрушающей проверки с помощью ультразвуковых, рентгеновских или инфракрасных технологий. Эти методы позволяют оценить внутреннюю структуру металлических и композитных материалов, не повреждая их. На заводах, где качественные характеристики продукции критически важны, данные технологии становятся стандартом. Ультразвуковая дефектоскопия, например, широко используется для определения трещин и пор в крупных металлических конструкциях. Большим плюсом является то, что эти методы могут применять на готовой продукции, не задерживая производственный процесс.
"Качество спорта на большей части производства, поскольку оно зависит от скорости и инноваций работы." — Инженер-механик Виктор Соловьев, конференция по инновациям в машиностроении 2023
Статистический анализ и программное обеспечение
Статистический процесс контроль (SPC) — это метод, который использует данные и анализ, чтобы стабильно поддерживать высокий уровень качества продукции. В SPC применяется программное обеспечение для сбора и анализа данных в режиме реального времени. Это позволяет инженерам быстро реагировать на возможные отклонения в производственных процессах. Например, при сборке крупных машин программное обеспечение может автоматически фиксировать малейшие отклонения от установленных стандартов и передавать эту информацию операторам, что позволяет немедленно исправлять любые ошибки. Программное обеспечение сегодня стало незаменимым инструментом в управлении качеством на любом современном заводе.
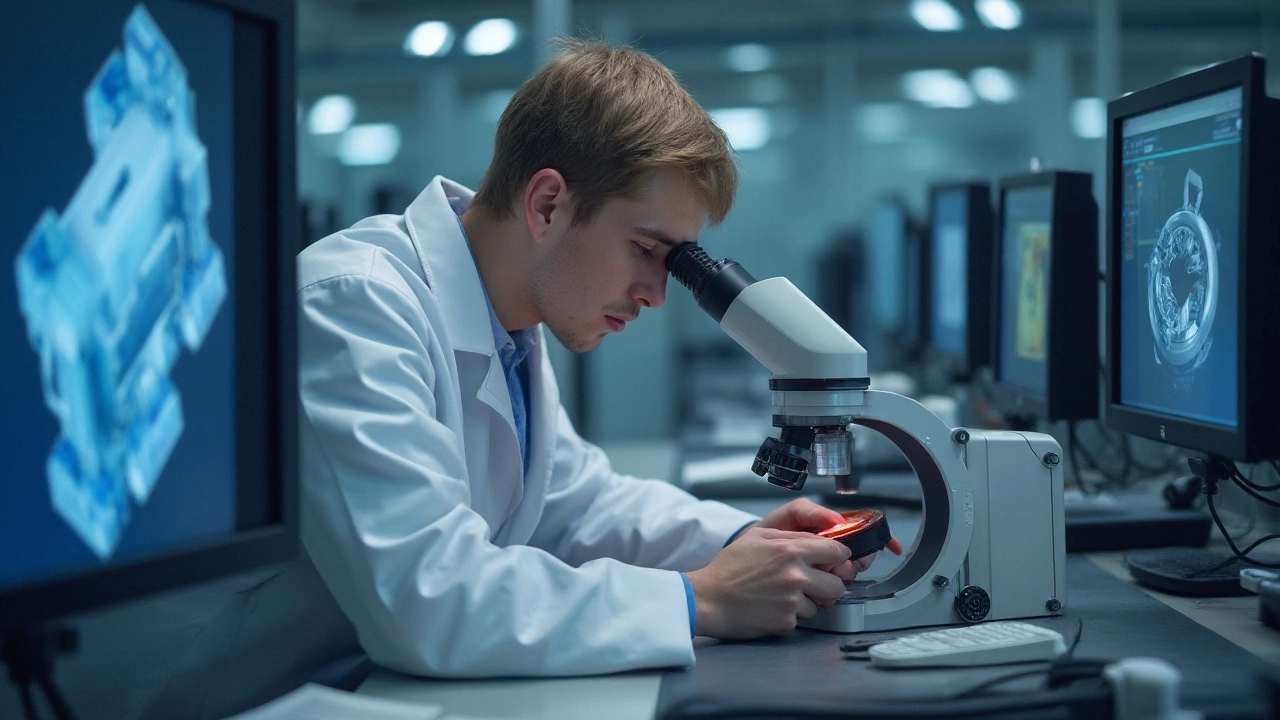
Преимущества и ограничения каждого метода
Контроль качества стал сердцем успешного производства в машиностроении, однако не все методы одинаково полезны в каждом сценарии. Начнем с традиционных методов контроля, таких как визуальная проверка. Преимущество этого метода в его простоте и скорости. Для профессионала с опытным глазом визуальная инспекция может выявить многие дефекты, которые не может обнаружить машина. Однако с ее популярностью связано несколько ограничений. Человеческий фактор — одна из главных слабых сторон визуальной инспекции. Усталость или небрежность инспектора могут привести к пропуску дефектов, что делает этот способ менее надежным по сравнению с автоматизированными системами.
Задачей неразрушающего контроля (NDT) является выявление скрытых проблем без нанесения ущерба компоненту. Этот метод предоставляет специалистам необходимые данные о состоянии материала или изделия, что делает его особенно важным на ранних этапах производства. Однако стоимость оборудования для NDT и требуемая подготовка специалистов могут стать серьезным барьером. Согласно отчету ассоциации ASTM International, использование NDT шло в авангарде, особенно в критических сферах авиакосмической промышленности и ядерной энергетики, где ошибки недопустимы.
"Контроль качества спасает жизни," — утверждает Джон Смит, эксперт в области неразрушающего контроля.
Автоматизированные системы набирают популярность благодаря своей точности и скорости. Они могут выполнять множество проверок за день, исключая человеческий фактор, что делает их выдающимися в средах с высоким объемом производства. Однако высокая стоимость таких систем и сложность их внедрения являются значительными ограничениями. Для небольших предприятий автоматизация может показаться недоступной роскошью. Тем не менее, для тех, кто может себе это позволить, внедрение автоматизированных систем работы с качеством может значительно увеличить производственную эффективность и снизить брак.
Заводские системы статистического процесс контроля, известные как SPC, позволяют контролировать стабильность и соответствие процессов путем анализа данных. Это позволяет обнаруживать и устранять отклонения на ранней стадии. Важным преимуществом SPC является возможность предсказуемости и повышение качества в процессе производства. Однако внедрение SPC требует от персонала навыков понимания сложных статистических данных, что требует времени и ресурсов для обучения. Многие предприятия уже осознали, что успех SPC зависит от уровня подготовки их сотрудников и культуры постоянного улучшения.
Роль автоматизации
В современном мире автоматизация стала ключевым элементом в повышении эффективности контроля качества в машиностроении. Это не просто дань моде или стремление к инновациям, а необходимость, продиктованная возрастающими потребностями рынка в быстрой, надежной и качественной продукции. Автоматизированные системы позволяют значительно снизить влияние человеческого фактора, улучшая точность и повторяемость процесса. За счет автоматизации значительно ускоряется процесс контроля, что в свою очередь, позволяет сократить сроки производства и снизить издержки.
Одним из заметных преимуществ автоматизации является возможность непрерывного мониторинга и оперативного реагирования на изменения производственного процесса. Например, использование датчиков и компьютеров позволяет в реальном времени собирать данные о параметрах продукции и моментально принимать корректирующие меры при отклонении от норм. Это особенно важно в условиях конкурентного рынка, где малейшие ошибки могут повлечь за собой большие потери.
"Автоматизация в сфере контроля качества оказывает серьёзное воздействие на конкурентоспособность предприятий, позволяя быстрее адаптироваться к изменениям и держать планку качества на заявленном уровне", — отмечают эксперты компании McKinsey.
Автоматизация также открывает дорогу к использованию современных технологий, таких как искусственный интеллект и машинное обучение, которые позволяют осуществлять не только контроль, но и прогнозирование возможных дефектов. Применение таких технологий делает возможным создание интеллектуальных систем, способных самообучаться и улучшать качество продукции с каждым циклом производства. Это становится особенно актуально в условиях массового производства, где количество единиц продукции исчисляется миллионами. Ни одна человеческая проверка не способна обеспечить такую же скорость и точность, как автоматизированная система.
Конечно, внедрение автоматизации требует начальных инвестиций, но зачастую уже в ближайшей перспективе они оправдываются экономией на издержках и улучшением качества продукции. Автоматизация помогает минимизировать ошибки, которые неизбежны в ручном управлении качеством. Это также обуславливает необходимость переквалификации персонала, так как работа с автоматизированными системами требует специальных знаний и навыков. Повышение квалификации работников становится важной задачей для компаний, решивших пойти по пути автоматизации.
Несмотря на все преимущества, следует помнить, что автоматизация – это не панацея. Она должна внедряться в комплексе с другими методами контроля качества. Успешное сочетание ручного и автоматизированного контроля позволяет достичь наилучших результатов и обеспечивает высокую конкурентоспособность компании на мировом рынке машиностроения. Грамотное использование автоматизации позволяет не только улучшить качество продукции, но и поднять уровень удовлетворенности клиентов, что в конечном итоге ведет к увеличению продаж и расширению бизнеса.
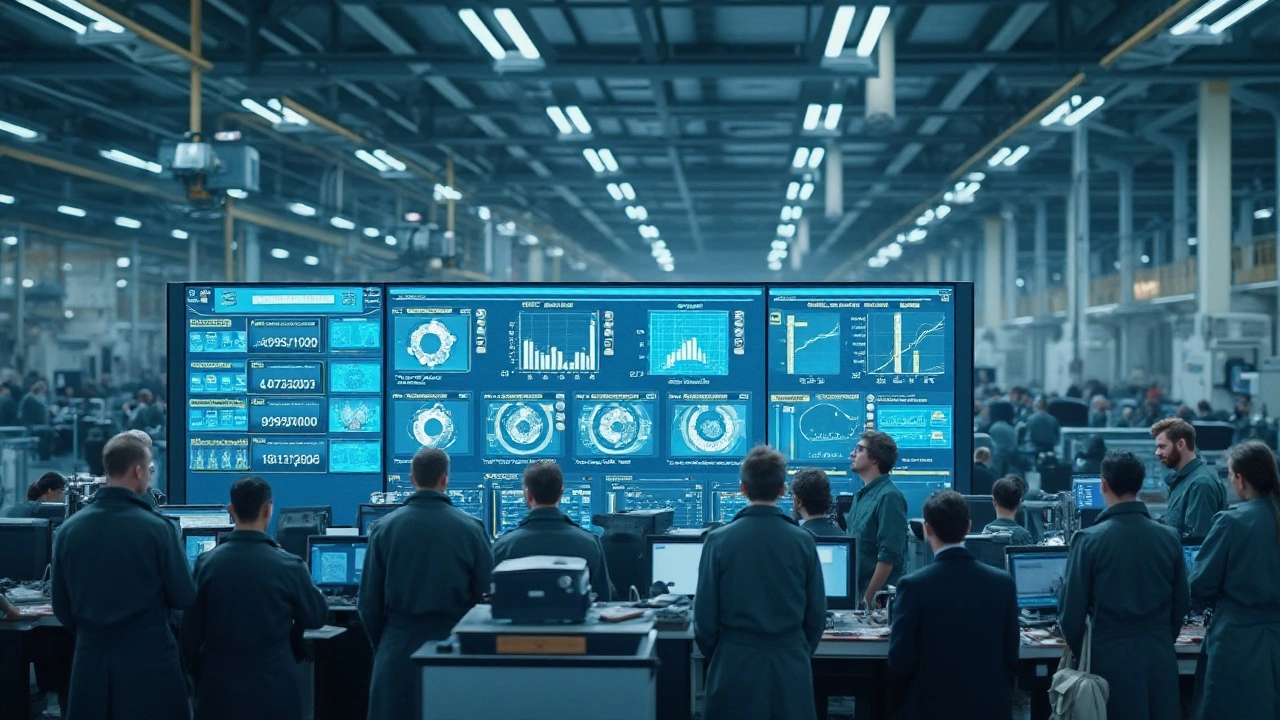
Статистический процесс контроль (SPC)
Статистический процесс контроль, или SPC, представляет собой метод анализа и мониторинга производственных процессов с использованием статистических методов. Применение SPC позволяет предприятиям машиностроения добиться высоких стандартов качества, выявляя отклонения в процессе и снижая вероятность брака на самых ранних стадиях. Особенностью SPC является его способность выявлять систематические ошибки, которые сложно обнаружить традиционными методами.
Эта методика основывается на сборе и анализе данных с целью выявления стабильности процесса. Использование графиков управления позволяет визуализировать изменения в процессе и определить, находятся ли они в пределах допустимого диапазона. На практике каждое предприятие выбирает свои показатели для контроля, но чаще всего это параметры продукции, такие как вес, размер, и другие физические характеристики. Такие данные помогают в выявлении как случайных, так и систематических отклонений, устранение которых становится возможным благодаря теме подходу.
Существует множество методов, применяемых в SPC, среди которых наиболее популярными являются контрольные карты и диаграммы распределения. Использование контрольных карт позволяет заметить незначительные изменения в процессе, на которые можно своевременно отреагировать. Американский инженер Уолтер Шухарт, который разрабатывал этот метод, утверждал, что практическое применение контрольных карт может существенно увеличить эффективность на производстве. Он писал:
"Грамотная интерпретация данных – это путь к снижению брака и повышению доверия к продукту как внутри компании, так и среди потребителей".
На сегодняшний день аналогичные технологии широко применяются не только в машиностроении, но и в электронной промышленности, а также в производстве потребительских товаров. Одной из сильных сторон подхода является возможность легкого распознавания изменений, которые могут повлиять на качество продукта, благодаря чему временные и ресурсные затраты снижаются на порядок. Такие известные предприятия, как Toyota и General Electric, уже давно используют SPC, что значительно помогает им в стремлении к совершенству и лидерству на мировом рынке.
Внедрение статистического контроля процессов на предприятии часто сопряжено с необходимостью обучения сотрудников. Понимание того, как интерпретировать контрольные карты и производить расчеты, помогает вовремя обнаружить проблему и найти эффективные пути её решения. Это требует определенных навыков, однако даже минимальные вложения могут окупиться много раз благодаря стабильности конечной продукции и уменьшению затрат.
Примечательно, что многие компании внедряют такие системы постепенно, начиная с самых простых методик анализа, что позволяет без лишней отягощения адаптироваться к новой системе и получить положительные результаты практически сразу после запуска. Постоянное улучшение процессов приносит значительные преимущества в условиях современного рынка, где от конкурентоспособности определяет успех в будущем. Таким образом, грамотное использование методов SPC прокладывает дорогу к более высоким стандартам качества на каждом этапе производства.
Внедрение и обучение персонала
Внедрение контроля качества в производственные процессы машиностроения — это задача, требующая комплексного подхода, включающего не только установку сложного оборудования, но и обучение сотрудников. Без этого даже самые передовые системы не смогут обеспечить нужный уровень качества продукции. Обучение начинается с основ понимания важности контроля качества. Каждый работник должен осознавать, как его действия влияют на конечный результат и качество производимого изделия. Специалисты в области качества проводят специальные семинары и тренинги, чтобы развить у сотрудников критическое мышление и внимание к деталям, которые необходимы для предупреждения дефектов.
В идеале обучение строится таким образом, чтобы каждый сотрудник, будь то оператор или инженер, мог понять, какие методы контроля качества наиболее эффективны на его участке работы. Например, визуальная инспекция, являющаяся одним из самых распространенных способов оценки состояния продукции, требует наличия специальных навыков и опыта. Человек должен не только замечать очевидные недостатки, но и предотвращать появление дефектов, которые в будущем могут стать серьезной проблемой.
"Качество не может быть случайным, — оно всегда является результатом продуманного процесса", — говорит Эдвардс Деминг, пионер в области управления качеством.
Не менее важным аспектом является интеграция автоматизированных систем контроля, которые требуют изучения программного обеспечения и технического обслуживания оборудования. Здесь на первый план выходит способность персонала работать с данными, которые предоставляют различные системы и сенсоры. Это может включать в себя анализ процессов, понимание статистики и умение предвидеть потенциальные сбои, используя данные. Такие навыки помогают не только в выявлении проблем, но и в оптимизации всего производственного процесса. Современные курсы повышения квалификации становятся важной частью корпоративной культуры, что способствует росту профессионализма и ответственности работников.
После прохождения обучения сотрудники должны регулярно проходить аттестацию для проверки их знаний и навыков. Это можно сделать через оценку эффективности работы каждого члена команды ощутимыми результатами производства. Например, снижение количества дефектной продукции после внедрения новой системы кондиционирования может стать показателем успешности обучения. Кроме того, компании могут внедрять программы наставничества, когда более опытные сотрудники помогают новичкам освоить сложные аспекты работы с системами контроля качества. Такой подход обеспечивает непрерывное развитие навыков и передачу знаний внутри организации.
Таким образом, при внедрении инструментов управления качеством обучение становится ключевым этапом, от которого зависит успех всего предприятия. Только через постоянное развитие профессиональных навыков и понимание новых технологий можно поддерживать высокий уровень качества и оставаться конкурентоспособными на современном рынке машиностроительной продукции.
Комментарии